Robotics Research: Can Robots Have Human-level Manipulation Skill?
Manipulation by hands and walking on feet are the two most significant kinetic skills of humans.
Robots appeared for the first time as technological products called industrial robots in 1962, and since then they have been numerously used in factories. Industrial robots are essentially mechanical arms and their manipulation skill is based on various special purpose grippers and tools for each specific task. Recently, advancement of non-industrial robots, especially humanoid robots with two legs, is taking place especially in Japan. People were surprised by the very natural walking skill of these humanoid robots. They made people feel the approach of an era where humans and robots coexist at home and in social spaces. One key technology among others for this expectation to happen is manipulation skill by multifingered human-like mechanical hands, since grasping and manipulation of various objects is a fundamental function for these robots to be useful
We have been studying basic technologies for grasping and manipulation of robotic mechanisms. Some results in our laboratory in this area will be introduced in the following.
(1) Control of Redundant Robot Manipulators.
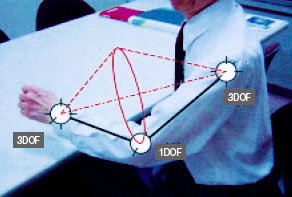
Figure 1: Locations of the seven degrees of freedom (DOF) in the human arm. Even after fixing the hand position and orientation, the elbow can move along a part of the circle shown in the figure, implying that the arm has one redundant degree of freedom.
A human arm can be regarded as a link mechanism with seven degrees of freedom. Since the task of holding an object and keeping it at an arbitrary position and orientation in three-dimensional space needs just six degrees of freedom, for this basic task the human arm has one more degree of freedom than necessary, which is hence called the redundant degree of freedom. A human utilizes this redundancy, often unconsciously, for taking a comfortable arm configuration for a given task, performing a manipulation task of an object behind an obstacle, and so on. Many robot arms are also designed to have redundant degrees of freedom to make it possible to perform a larger array of tasks. However, to make this arm work possible, it is of course necessary for an engineer to clearly recognize the purpose of redundancy utilization and to select an appropriate arm trajectory. For this problem we have proposed the task-decomposition approach in which the whole task is decomposed into several subtasks with an order of priority and each subtask with higher order is realized first by utilizing a general kinematic solution of the arm motion. Since the degrees of redundancy of humanoid robots are generally far larger than conventional industrial robots, much more study on redundancy utilization will be necessary.
(2) Manipulability
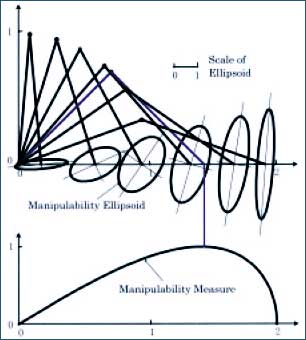
Figure 2: Manipulability ellipsoid and manipulability measure of a two-joint arm. The blue arm configuration with a right elbow angle attains the maximum manipulability measure.
In designing the mechanism of a robot arm or in planning the arm posture for performing a task, one important factor that should be taken into account is the ease of arbitrarily changing the position and orientation of the end effector at the tip of the arm. To give a quantitative index of this ability, the concept of manipulability was proposed. This is based on the idea that, when we consider the set of all endeffector velocities that are realizable by joint velocities under a magnitude constraint (i.e., the Euclidean norm is not larger than one), it is desirable that this set is large and Spherical as much as possible. For example, consider a very simple case of a two-joint arm moving in a plane, then this set becomes an ellipse (called manipulability ellipsoid). Regarding the area of this ellipse as a measure of manipulation ability of the arm (called manipulability measure), we can show that this measure takes its maximum when the elbow angle is a right angle, and when the lengths of upper arm and forearm are the same if the total arm length is constant. These results are intuitively natural when we consider our arm moving on a table.
(3) Analysis and Control of Grasping and Manipulation by Robot Hands
In grasping and manipulating an object by a multi-fingered robot hand, many contact points and contact forces between the hand and the object are generally involved. This causes the arbitrariness of the internal force, which can be utilized for securing the grasp against various external disturbance forces. In order to make the determination of the internal forces more systematic, we proposed a physically reasonable definition of grasping and manipulating forces for multi-fingered robot hands. We also proposed the concept of active closure and passive closure to classify robotic mechanisms from the viewpoint of how the mechanism constrains the grasped object. Active closure means a grasp that needs a feedback control based on the object's position and force, and passive closure means a grasp that does not. These concepts will make the planning of grasping and manipulation procedure for robots much more reasonable.
(4) Understanding Human Skill Using Haptic Virtual Reality Technology
Automation of assembly tasks by robots is still very hard, despite the fact that a human operator can perform the task without much difficulty. If we understand this human skill better, it will be easier to automate assembly tasks. But it is often the case that the operator cannot describe his/her skill explicitly. It is also rather difficult to measure motion, force, contact state, and so on during the execution of the real task. To overcome this difficulty, we developed a virtual task environment using haptic virtual reality technology. A peg-in-hole task in virtual space was provided using this system. By a comparison study, we saw that although the virtual task needs twice as much time as the real task, the order of the three motions required to perform the task using three assembly strategies is almost the same in the real and virtual tasks, implying that the virtual task environment could be valid for qualitative study of human skill. We are also working on improving the performance of haptic display devices from several aspects.
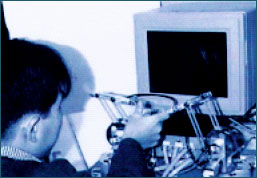
Figure 3: Human skill observation using haptic virtual reality technology. The operator can perform a virtual peg-in-hole task getting the feel of touch through his fingers.
In our laboratory, we are also working on other robotics-related research topics such as modeling and control of flexible manipulators, analysis and control of master-slave manipulator systems, mixed reality, development of rescue systems, and legged robots.
I believe that there is a strong possibility that diffusion of intelligent mechanical systems like robots will change our lifestyles drastically in the near future. I hope that many young people will become interested in robotics and contribute to the research and development of robots that will be useful for mankind.
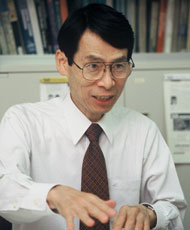
Tsuneo Yoshikawa
Born in 1941
Specialized Research Field: Robotics, Mechanical Control Engineering
Graduate of the doctoral program, Graduate School of Engineering, Kyoto University
D.Eng., Kyoto University
Professor, Graduate School of Engineering, Kyoto University
URL http://mech-server.mech.kyoto-u.ac.jp/lab/yoshikawa/ (External Link)
"Can you imagine what the world might be like if robots were to come into possession of psyches? One important aspect of the work being done by we who research robotics is defining the future of robots, or a vision of that future. "
The most interesting recent development in robotics concerns humanoid robots. Prof. Yoshikawa's research, on the other hand, involves manipulatory systems, of which perhaps the best known example is the human hand. While this field has traditionally focused on industrial applications, the professor's work in this regard is now considered to be a key element in determining the future outlook for humanoid robots. For acquiring the ability to "work with objects", that is, to grab and manipulate them, is essential if robots are to become truly useful in human society.
Unlike many roboticists, Prof. Yoshikawa, whose original specialty is control theory, did not enter the field out of any childhood fascination with children's robot superhero programs. Accordingly, he is not optimistic about the relationship between humans and robots, instead ceaselessly emphasizing the need for constant examination of the policies of robotics research and development. The professor's awareness of the tremendous impact of science and technology gives him an equally tremendous sense of responsibility vis-a-vis society, in his capacity as a scientist. Prof. Yoshikawa's voice is lively and his eyes alight when he speaks of his robotics research, much like an innocent little boy's would be under similar circumstances. That very enthusiasm may give us all hope for peaceful coexistence on the part of humans and robots.
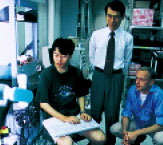
Prof. Yoshikawa advises students regarding their experiments. The Yoshikawa Lab adopts a one research topic per person approach, wherein students choose their own research topics for their theses, an approach that places much store by the originality of students' ideas.